Revolutionizing Manufacturing with Electrical Plastic Molding
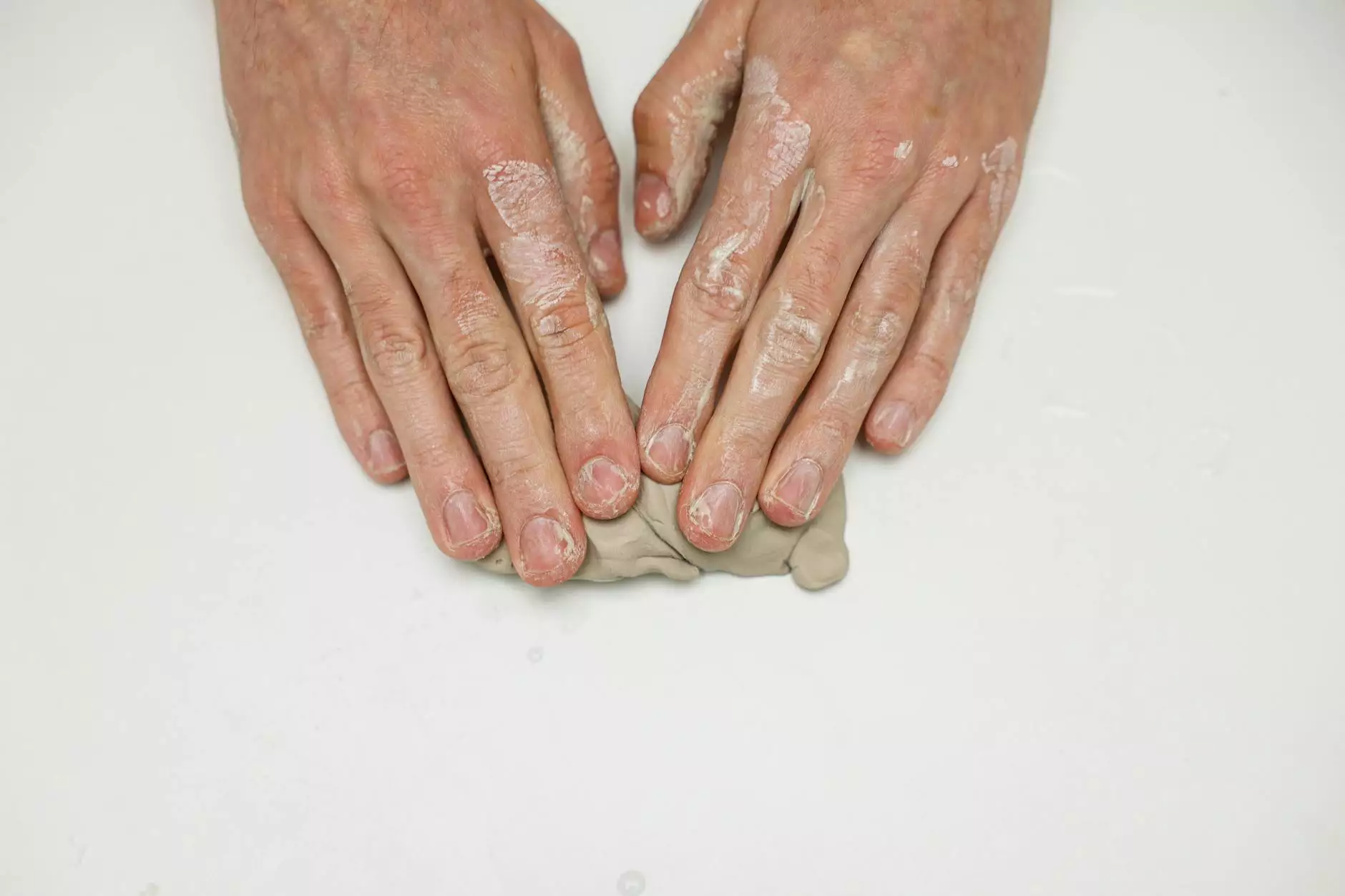
The evolution of manufacturing processes has led to numerous advancements in the way components are produced, particularly in the context of Electrical Plastic Molding. This technique is not just a cornerstone of modern engineering; it represents the pinnacle of efficiency, accuracy, and innovation in today’s competitive business environment. In this article, we will explore the intricate details of Electrical Plastic Molding, its applications, benefits, and why it is a game-changer for industries ranging from consumer electronics to automotive manufacturing.
The Basics of Electrical Plastic Molding
Electrical Plastic Molding refers to a manufacturing process that involves shaping plastic materials using electrical energy, typically via an injection molding machine. This method is crucial for producing intricate designs and high-precision parts required in various applications. The core steps in the process include:
- Material Selection: Choosing the right type of plastic, often thermoplastic polymers, which can be molded at high temperatures.
- Melting: Heating the plastic to a liquid state to prepare it for molding.
- Injection: Injecting the molten plastic into a mold cavity under high pressure.
- Cooling: Allowing the material to cool and solidify within the mold.
- Demolding: Removing the finished part from the mold.
This process not only enhances precision in manufacturing but also significantly reduces production time and costs, making it a preferred choice for manufacturers worldwide.
Applications of Electrical Plastic Molding
One of the most compelling aspects of Electrical Plastic Molding is its versatility. This technique finds applications across various industries, including:
1. Consumer Electronics
With the rapid advancement of technology, the demand for lightweight, durable components has surged. Electrical Plastic Molding is indispensable in creating parts for smartphones, tablets, and other electronic devices, where precision and aesthetics are paramount.
2. Automotive Industry
In the automotive sector, molded plastic components are used extensively, from dashboard assemblies to intricate wiring harnesses. The durability and lightweight characteristics of molded plastics help improve fuel efficiency and vehicle performance.
3. Healthcare
The healthcare industry relies on molded plastics for a variety of applications, including medical device housings, surgical instruments, and disposable syringes. The precision and quality control afforded by Electrical Plastic Molding are crucial for ensuring safety and efficacy.
4. Aerospace
The aerospace industry benefits from this technology through the production of lightweight yet strong components. These include interior panels, structural elements, and storage compartments that contribute to overall aircraft efficiency.
Advantages of Electrical Plastic Molding
Understanding the benefits of Electrical Plastic Molding is essential for businesses considering this manufacturing approach. Here are the key advantages:
1. Enhanced Precision
One of the most significant advantages is the high level of precision it offers. The injection molding process allows for tolerances as tight as ±0.005 inches, which is critical for applications that require exact specifications.
2. Cost-Effectiveness
Although the initial investment in molding equipment can be substantial, Electrical Plastic Molding drastically reduces long-term production costs through lower material waste and quicker production cycles. The ability to produce large quantities of identical items makes it highly economical.
3. Design Flexibility
The versatility of Electrical Plastic Molding also enables engineers to design complex geometries that would be impossible to achieve with traditional manufacturing methods. This opens up new possibilities for product innovation and functionality.
4. Sustainability
Manufacturers are increasingly focusing on sustainability, and molded plastics can be engineered to be recyclable. This aspect corresponds with global trends toward eco-friendliness, making Electrical Plastic Molding a responsible choice for modern manufacturers.
Your Partner in Electrical Plastic Molding: DeepMould.net
At DeepMould.net, we pride ourselves on being at the forefront of the Electrical Plastic Molding industry. Our state-of-the-art facilities and team of experienced professionals enable us to produce high-quality plastic components that meet and exceed our clients' expectations. Here’s what sets us apart:
- Advanced Technology: We utilize the latest molding technology to ensure precision and efficiency.
- Skilled Workforce: Our team consists of skilled engineers and technicians dedicated to producing the best possible products.
- Customer-Centric Approach: We work closely with our clients to tailor solutions to their specific needs, ensuring satisfaction and success in every project.
- Continuous Improvement: We are committed to ongoing research and development, constantly seeking ways to enhance our processes and offerings.
Future Trends in Electrical Plastic Molding
As technology continues to advance, the field of Electrical Plastic Molding is set to evolve as well. Key trends to watch include:
1. Smart Manufacturing
The integration of IoT (Internet of Things) solutions in molding processes will facilitate smarter factories. This will enhance efficiency through real-time monitoring and predictive maintenance.
2. Biodegradable Materials
With the growing awareness of environmental issues, the demand for biodegradable plastics is increasing. The development of eco-friendly materials suitable for molding will become a significant trend in the industry.
3. Automation and Robotics
Automation will play a critical role in enhancing production speed and consistency. The adoption of robotics in Electrical Plastic Molding can streamline the manufacturing process, reducing labor costs and human error.
Conclusion
In conclusion, Electrical Plastic Molding is an essential manufacturing process that offers unparalleled advantages and opportunities for various industries. Its precision, cost-effectiveness, and design flexibility make it a premier choice for companies looking to innovate and stay competitive in today’s dynamic market.
At DeepMould.net, we are committed to leveraging the power of Electrical Plastic Molding to help businesses achieve their manufacturing goals while maintaining the highest standards of quality. As we move forward, embracing trends and innovations within this field will enable us to continue providing superior solutions that empower our clients to thrive in an ever-evolving landscape.