Revolutionizing Flight: The Magic of 3D Printed Wings
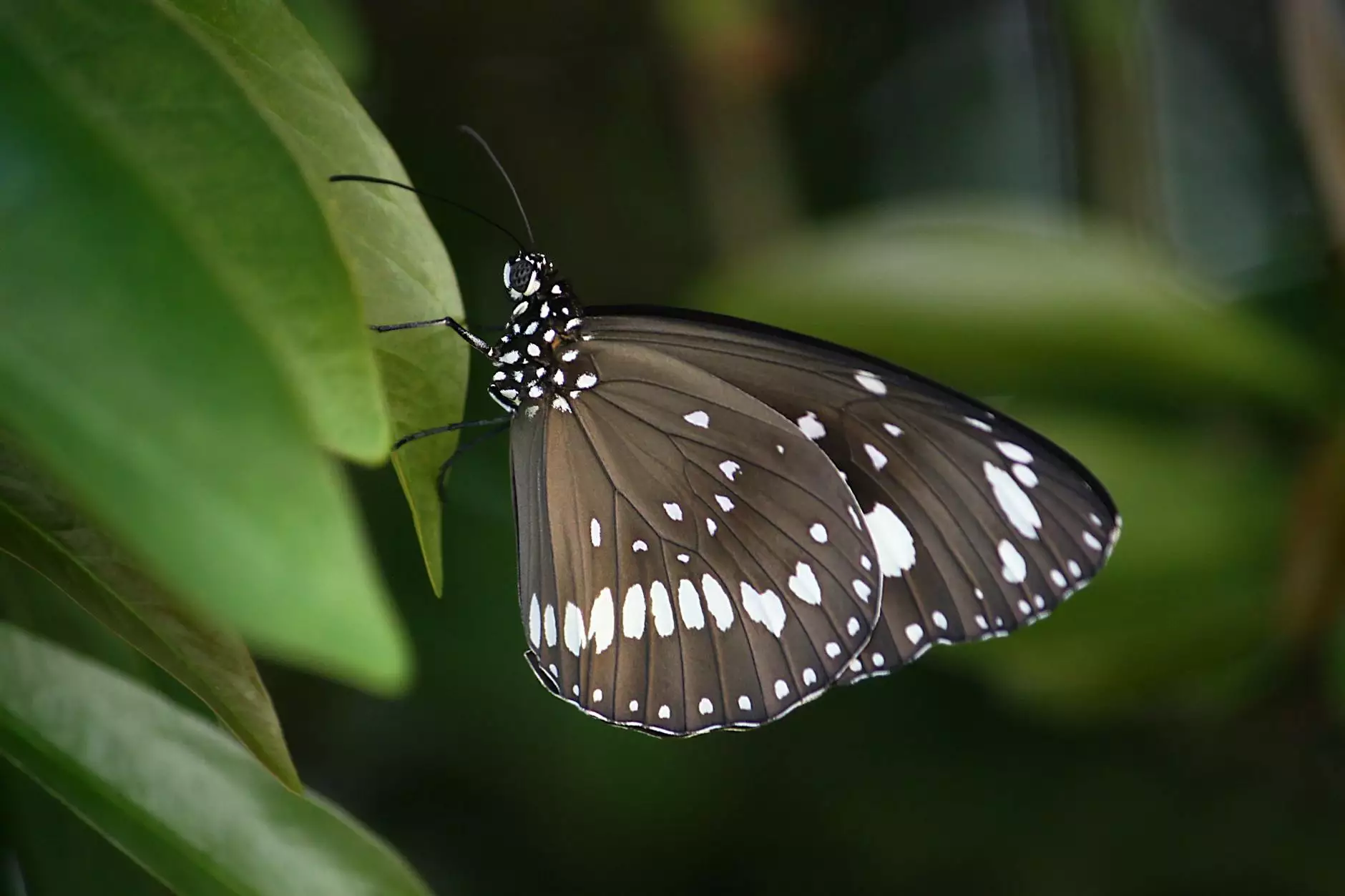
The world of aviation is undergoing a monumental transformation, and at the forefront of this shift is the innovative technology of 3D printed wings. As the aerospace industry embraces advanced manufacturing techniques, the efficiency, customization, and sustainability offered by 3D printing are becoming crucial. This article delves deep into the realm of 3D printed wings, examining their benefits, applications, and the future of flight that they herald.
Understanding 3D Printing in Aerospace
3D printing, also known as additive manufacturing, is a process that creates three-dimensional objects by layering materials based on digital models. This technology has been a game-changer for many industries, including aerospace. By allowing for the production of complex geometries and lightweight structures, 3D printing is paving the path for creating high-performance components, such as 3D printed wings.
The Process of Creating 3D Printed Wings
The journey of manufacturing 3D printed wings begins with a detailed digital model. This model is typically created using computer-aided design (CAD) software, where engineers and designers can manipulate the design to maximize performance and minimize weight.
Once the design is finalized, the next steps are:
- Material Selection: Various materials like thermoplastics, metals, and composites can be used depending on the desired strength and properties.
- 3D Printing Techniques: Techniques such as Fused Deposition Modeling (FDM) or Selective Laser Sintering (SLS) can be employed.
- Post-Processing: After printing, wings may require sanding, polishing, or coatings to enhance their aerodynamics and durability.
The Advantages of 3D Printed Wings
3D printed wings bring several advantages over traditional manufacturing methods. Here are some key benefits:
1. Weight Reduction
One of the standout benefits of 3D printed structures is their ability to be lighter than traditionally manufactured parts. Weight savings are critical in aviation, where every ounce counts. By utilizing complex designs that incorporate lattice structures and conformal shapes, engineers can reduce weight without compromising strength.
2. Design Flexibility
3D printing allows for greater design freedom, enabling aerodynamics engineers to create shapes that were previously impossible or prohibitively expensive to produce. 3D printed wings can include integrated systems and features that are not possible with conventional manufacturing techniques.
3. Customization and Performance
Customization is a game changer in the aerospace sector. Different flight missions may require different wing characteristics. 3D printing makes it feasible to quickly adapt designs for specific airframes or missions. This cater to unique specifications and performance demands with speed and efficiency.
4. Reduced Lead Times
Traditional manufacturing often involves lengthy lead times due to tooling and setup requirements. In contrast, 3D printing can significantly reduce the time from design to production. This agility ensures that aircraft can be modified rapidly to meet evolving requirements.
Applications of 3D Printed Wings
The applications of 3D printed wings are vast and varied, impacting both commercial and military aviation.
1. Prototyping and Testing
3D printing provides an invaluable tool for prototyping. Aerospace engineers can quickly produce wing models to conduct wind tunnel testing and simulation, allowing for iterative design improvements.
2. Small Aircraft and Drones
The drone industry has particularly embraced 3D printed wings. By utilizing lightweight materials and customized designs, drone manufacturers can enhance flight performance and efficiency, allowing for greater payload capacities and longer flight times.
3. Repair and Maintenance
Imagine the ability to produce replacement parts on-demand! 3D printing facilitates the rapid production of wing components for maintenance needs. This reduces downtime and enhances fleet operational capability.
4. Commercial Aircraft Innovations
Leading aerospace companies are investing in the research and development of 3D printed wings for new commercial aircraft designs. This innovation promises to redefine efficiency and performance in the next generation of flight.
Environmental Impact and Sustainability
As the world becomes more environmentally conscious, the aerospace industry must also adapt. 3D printed wings present a pathway towards sustainability through:
- Material Efficiency: 3D printing minimizes waste as materials are added layer by layer.
- Lightweight Structures: Reducing weight leads to lower fuel consumption and emissions during flights.
- Localized Production: 3D printing can be done closer to the point of use, reducing transportation emissions and costs.
Challenges and Considerations
Despite the numerous advantages, the adoption of 3D printed wings does come with challenges:
1. Certification and Regulations
The aerospace industry is one of the most regulated sectors in terms of safety. Gaining certification for new materials and manufacturing processes can be a lengthy and complex process.
2. Material Limitations
While advancements are being made, not all materials used in traditional manufacturing have a direct equivalent in 3D printing. Finding materials that meet the strength and durability requirements for critical components like wings is essential.
3. Skills and Training
The workforce must adapt to this new technology. Training and developing skills in 3D printing technology is vital to ensure that engineers and manufacturers can successfully implement these new processes.
The Future of 3D Printed Wings
The future of 3D printed wings is bright as technological advancements continue. From improved materials to faster printing speeds, the possibilities are expanding:
- Research and Development: Investment in R&D will lead to novel designs and better materials.
- Integration with AI: 3D printing processes can potentially integrate with AI to optimize designs continuously.
- Mass Customization: The ability to mass-produce customized wings for various aircraft types will likely become a reality.
Conclusion
In summary, the advent of 3D printed wings is heralding a new era in aviation, characterized by enhanced efficiency, design flexibility, and sustainability. As the technology continues to evolve, it promises not just to change how wings are manufactured but to revolutionize the entire aerospace industry. The future of flight is not just about soaring through the skies—it's about doing so in a way that respects our planet and paves the way for innovations yet to be imagined. The adoption and exploration of 3D printed wings will undoubtedly lead to breakthroughs that will define the next decade of aviation.
For more insights into the world of 3D printing and how it is shaping industries, visit 3DPrintWig.com.