Understanding Plastics Injection Molding: A Key Player in Modern Manufacturing
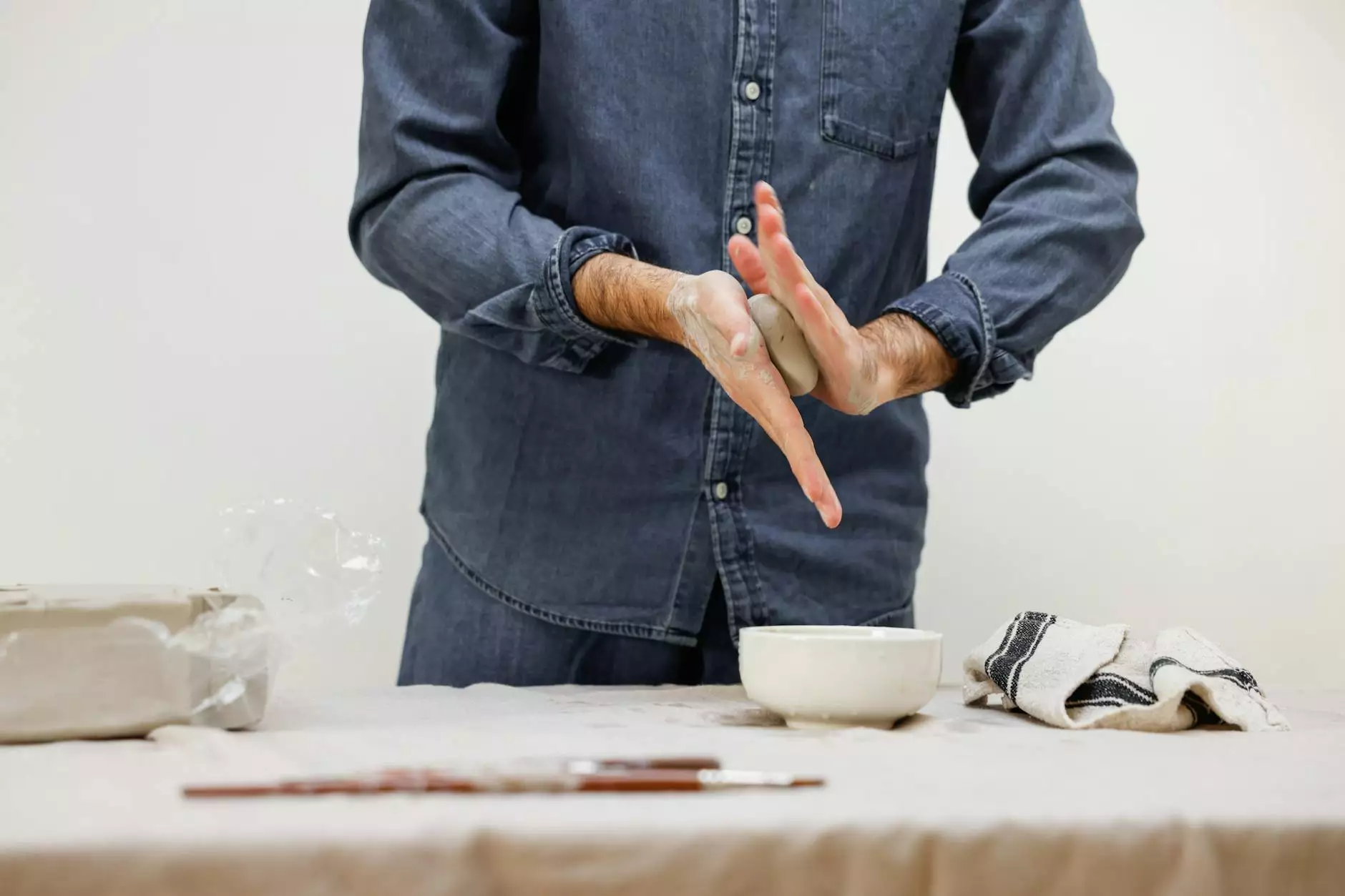
Plastics injection molding stands as one of the most transformative manufacturing techniques in today's industry. This innovative process allows for the mass production of plastic components, making it an indispensable technology for countless sectors, from automotive to consumer goods. In a world where efficiency and precision are paramount, understanding this method is crucial for businesses looking to enhance their production capabilities.
What is Plastics Injection Molding?
At its core, plastics injection molding involves the injection of molten plastic material into a pre-designed mold. The process can be broken down into several essential stages:
- Material Preparation: Raw plastic pellets or granules are fed into a heated barrel.
- Melt and Injection: The pellets are melted and then injected into a mold cavity under high pressure.
- Cooling: The molten plastic cools and solidifies while inside the mold.
- Demolding: Once the plastic has hardened, the mold opens, and the finished part is ejected.
This process is not only efficient but also allows for incredible flexibility in design, making it possible to produce complex shapes that would be difficult or impossible to create using other manufacturing methods.
The Advantages of Plastics Injection Molding
The advantages of plastics injection molding are numerous, providing significant value for manufacturers and end-users alike. Some of the most notable benefits include:
- High Efficiency: Injection molding can produce large volumes of parts quickly and consistently, reducing manufacturing time.
- Cost-Effective Production: Once the mold is created, the cost per part decreases significantly with mass production.
- Complex Geometries: The process allows for intricate designs that are hard to achieve with other methods.
- Material Versatility: A wide range of thermoplastics and thermosetting materials can be used in the injection molding process.
- Reduced Waste: The precision of the method minimizes excess material, contributing to environmentally friendly practices.
Applications of Plastics Injection Molding
The versatility of plastics injection molding opens doors to a plethora of applications across various industries. Here are some key areas where this technology excels:
1. Automotive Industry
The automotive sector heavily relies on injection molding to produce components such as dashboards, door panels, and connectors. The lightweight characteristics of plastic parts combined with their strength contribute to improved fuel efficiency and vehicle performance.
2. Consumer Electronics
From smartphone casings to intricate circuit components, plastics injection molding is at the heart of consumer electronics manufacturing. This technology allows manufacturers to produce aesthetically appealing and durable products at scale.
3. Medical Devices
The healthcare sector demands precision and reliability, making plastics injection molding ideal for creating syringes, surgical tools, and device housings. These products frequently require strict compliance with health regulations, which the injection molding process can efficiently meet.
4. Packaging Solutions
Injection molded plastics are used in packaging due to their durability and practicality. Items such as containers, bottles, and closures benefit from the strength and lightweight properties of the materials used.
The Role of DeepMould in Plastics Injection Molding
DeepMould, a leading player in the field of metal fabrication, extends its expertise into the realm of plastics injection molding, providing comprehensive solutions that address the needs of a diverse clientele. The company's commitment to innovation and quality ensures that they deliver unparalleled products and services in this competitive market. Here’s how DeepMould sets itself apart:
Expert Engineering
DeepMould employs seasoned engineers who specialize in mold design and development. This expertise ensures that the molds produced are not only efficient but also conducive to high-quality output.
State-of-the-Art Technology
The company harnesses the latest technological advancements in machining and molding processes. By staying updated with the industry trends, DeepMould is able to maximize production efficiency while minimizing costs.
Customized Solutions
Understanding that each client has unique requirements, DeepMould offers tailored solutions for plastics injection molding. Whether it's for prototyping or full production runs, the company is equipped to meet specific demands.
Choosing the Right Material for Plastics Injection Molding
The choice of material is critical in the injection molding process. Various plastics can be used, depending on the desired characteristics of the final product. Here are some common materials utilized:
- Polypropylene (PP): Known for its flexibility and resistance to chemicals.
- Polycarbonate (PC): Offers high impact resistance and is often used in safety equipment.
- ABS (Acrylonitrile Butadiene Styrene): Balances strength and toughness, commonly found in consumer products.
- Nylon: Ideal for applications requiring strength and thermal stability.
The right material ensures that the resulting part will meet performance expectations while achieving desired aesthetics.
The Process of Mold Design and Development
Creating efficient molds is a critical step in the plastics injection molding process. Here’s a deeper look at the necessary considerations:
Design for Manufacturability (DFM)
Integrating DFM principles during the design phase can significantly streamline the production process. Key factors include:
- Part Geometry: Simplifying shapes can reduce costs and improve manufacturability.
- Tolerances: Setting achievable tolerances ensures parts fit together correctly, minimizing rework.
- Mold Flow Analysis: Simulating the injection process helps predict and eliminate potential issues, leading to more successful mold designs.
Mold Fabrication
Once the design is finalized, the fabrication of the mold includes:
- Machining: Employing CNC machines to shape the mold components precisely.
- Assembly: Integrating various mold parts, ensuring proper alignment and fit.
- Testing: Performing trial runs to identify any design flaws and make necessary adjustments.
Conclusion: The Future of Plastics Injection Molding
As industries continue to evolve, plastics injection molding will play a pivotal role in pushing modern manufacturing towards greater efficiency and sustainability. Innovations in materials, machinery, and design processes are set to enhance the capabilities of injection molding even further.
For businesses in the metal fabricators' space, like DeepMould, the integration of injection molding techniques provides a competitive advantage, improving product offerings and enabling them to meet diverse client needs effectively.
In a landscape where quality and speed are crucial, mastering plastics injection molding will ensure lasting success and drive future growth within the manufacturing sector.